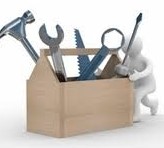
Lean tools
Lean methodology is materialized through the application of series of techniques, which have been successfully implemented in companies in different sectors. These techniques can be implemented independently or jointly.
A good way to simplify and order these techniques is to group them into three different groups. The first group are those techniques that, due to their characteristics, clarity and possibility of implementation are easily and directly applicable in any sector. The action is usually “common sense”.
- The 5’S: Technique used to improve working conditions through excellent organization, order, standardization and cleanliness in each area.
- SMED: System used to reduce preparation times.
- Standardization: A technique that seeks to develop written instructions that show the best way to act.
- TPM: A set of multiple actions of total productive maintenance that seeks to eliminate losses due to downtime of the machines.
- Visual control: A set of visual control and communication techniques that aim to make it easier for everyone to know the state of the system.
The second group are the techniques that require a greater commitment of company’s part.
- Jidoka: Technique based on the incorporation of the ability of machines to detect that they are producing errors.
- Quality techniques: A techniques set that pursue the reduction and elimination of defects.
- Staff participation systems (SPP): Organized workgroup systems that supervise and improve the Lean system.
The last group includes the most specific techniques that change the way production that is planned, programmed and controlled. They require specialized resources and involve the maximum application of the JIT paradigm.
- Heijunka: A techniques set that serve to plan and level the customers demand, in volume and variety, and allow the evolution towards production in continuous flow.
- Kanban: Synchronized control and programming system of card-based production.
There is a very large range of Lean tools, here we only mention the most common.